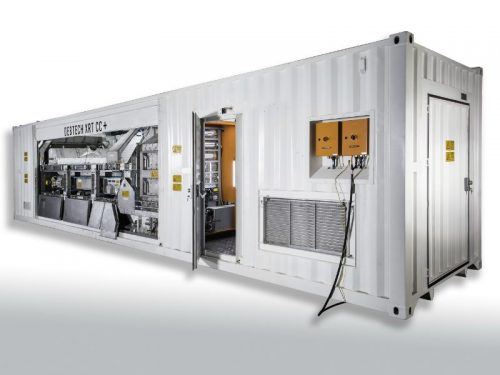
The two x-ray transmission (XRT) coarse concentrator plus (CC+) units were designed and manufactured by De Beers Technologies (DebTech) at its facilities near Johannesburg, and will be commissioned at Jwaneng by the end of 2018.
Located 120 km from Botswana’s capital Gaborone, Jwaneng is owned by Debswana – a joint venture between the Republic of Botswana and De Beers Plc; it is one of the world’s most valuable diamond mines by reserve value.
“The XRT CC+ units at Jwaneng are upscaled versions of our XRT coarse concentrator model,” says Gordon Taylor, head of DebTech.
“When initially considering Jwaneng’s requirements, we felt confident, given our history of developing these types of machines, that we could engineer the best solution for them.”
The two CC+ ore sorters form the heart of a new large diamond recovery pilot plant at Jwaneng.
Design and construction of the XRT CC+ units began in January 2017 and they were delivered to Debswana in January 2018 for early integration into the plant.
What makes this application different from the typical application of the ore sorting units, says Taylor, is the position of the units right at the front end of the plant.
Generally, they are located further down the process, where throughput requirements are not as onerous.
“This installation, on the other hand, will be treating coarse sized run-of-mine (ROM) material, so must handle substantial throughput quantities of up to 500 tph,” he says.
While it has long been considered quite likely that the Jwaneng pipe could contain large diamonds, previous processing techniques did not lend themselves to a simple elegant recovery system.
“The recent development of more cost-effective processing techniques based on improved XRT technology has changed the economics of finding larger diamonds,” he says.
The XRT technology is also valuable for replacing coarse and middles dense media separation (DMS), says Taylor, as the typical XRT concentrate yield is significantly less than an equivalent DMS plant.
“This considerably reduces downstream infrastructure.”
“XRT consumes much less power and water, does not require a consumable material such as ferrosilicon and is much more accurate at identifying and sorting diamonds,” indicates Taylor.
In the XRT sorting unit, material enters the unit via the inlet chute and is transported by the feeder to an internal conveyor belt, where it passes between the X-ray source and the X-ray camera.
The camera images are analysed by software algorithms and – if a diamond is identified – then a pneumatic ejection system is activated to divert the stone to a concentrate chute.
“The system provides continuous x-ray transmission images of material being processed, and these images are used to accurately discriminate between material types,” he says.
“The ‘Dual Energy’ feature on XRT sorting systems is a further enhancement that improves the technique’s ability to analyse materials of differing thickness.”
The powerful imaging capabilities of the system allows not only identification and ejection of diamonds – be they low-luminescent, type II, coloured or boart – but the generation of online carat estimates and stone count values.
He also highlights the accuracy of the latest XRT technology in the CC+ units in efficiently treating large volumes of material.
“The latest XRT technology minimises the number of ‘false positives’ that the system identifies, and therefore cuts down drastically on the amount of mined material that must be unnecessarily accommodated in downstream processing capacity,” he says.
“This accuracy transforms the economics of the whole process, and makes for much more efficient minerals processing.”
Supplied in 12 m shipping containers, the CC+ units are designed to conveniently include all the related technology and services that the customer will need to operate the plant.
The containerised solution generally requires only an electrical power source and a water connection.
Each sorter is self-contained with its own dedicated control room, internal water and electrical power conditioning, and internal compressed air generation.
Ease of use is ensured by a user-friendly, menu-driven control interface for the operator and the machines are fully integrated into the plant control system.
“The containerised configuration means that we can construct and test the machines under controlled workshop conditions, ensuring that all aspects are ready for commissioning by the time the unit leaves our facilities,” says Taylor.
“Containerisation also makes it simpler to transport the units to site and to off-load, while reducing commissioning time considerably.”
DebTech will also be supplying full maintenance support for the CC+ units, which are fitted to provide remote diagnostics.
“In summary, the XRT CC+ sorters supplied to Jwaneng will optimise diamond recovery with minimum gangue material at high feed-rates, while providing the customer with the highest chances of recovering large stones,” says Taylor.